The displacement transducer, also known as the "Eddy current" probe, is usually used for low frequency measurements (below 1,000 Hz) in turbomachinery journal bearings. Proximeters are used to measure the shaft radial or axial displacement.
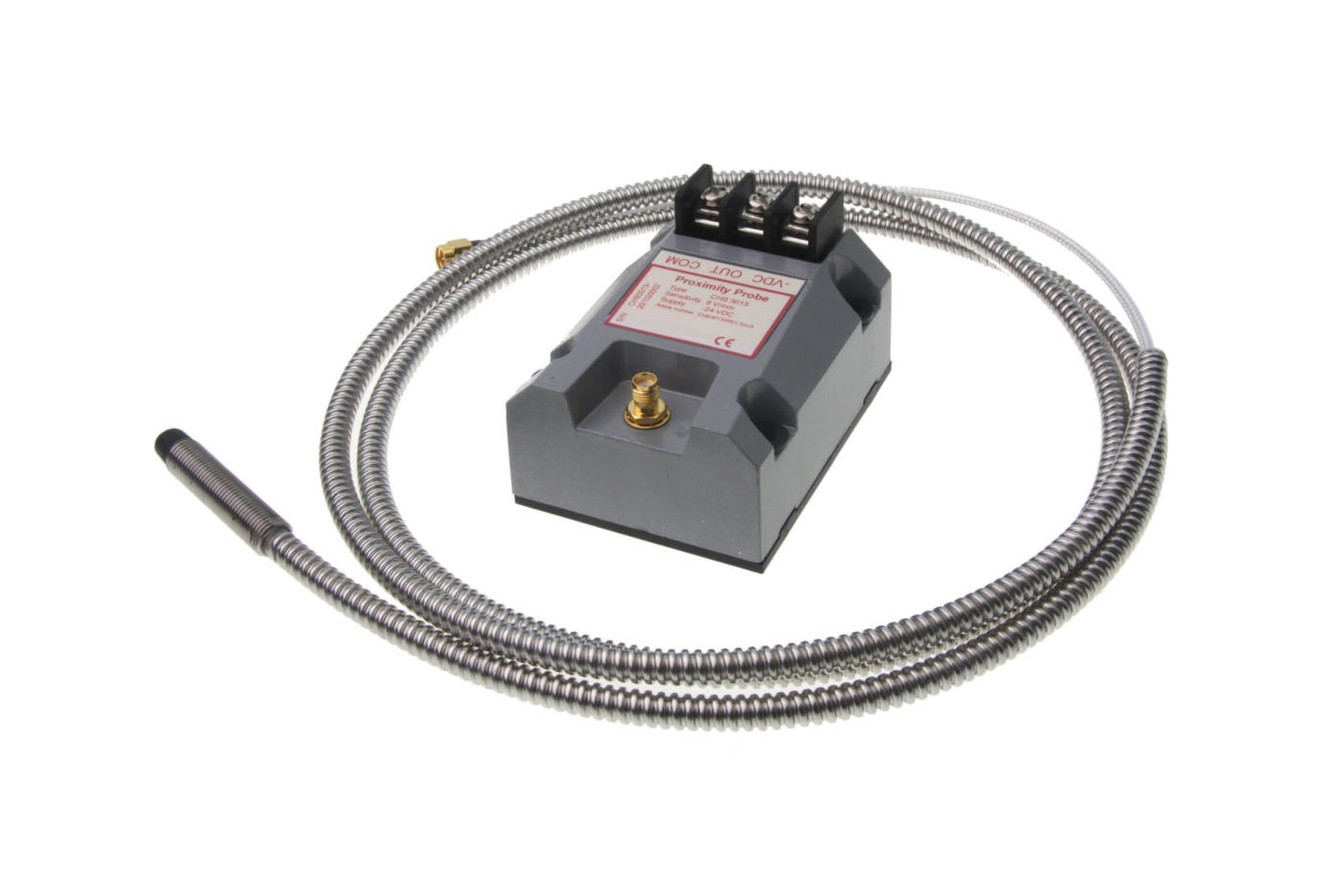
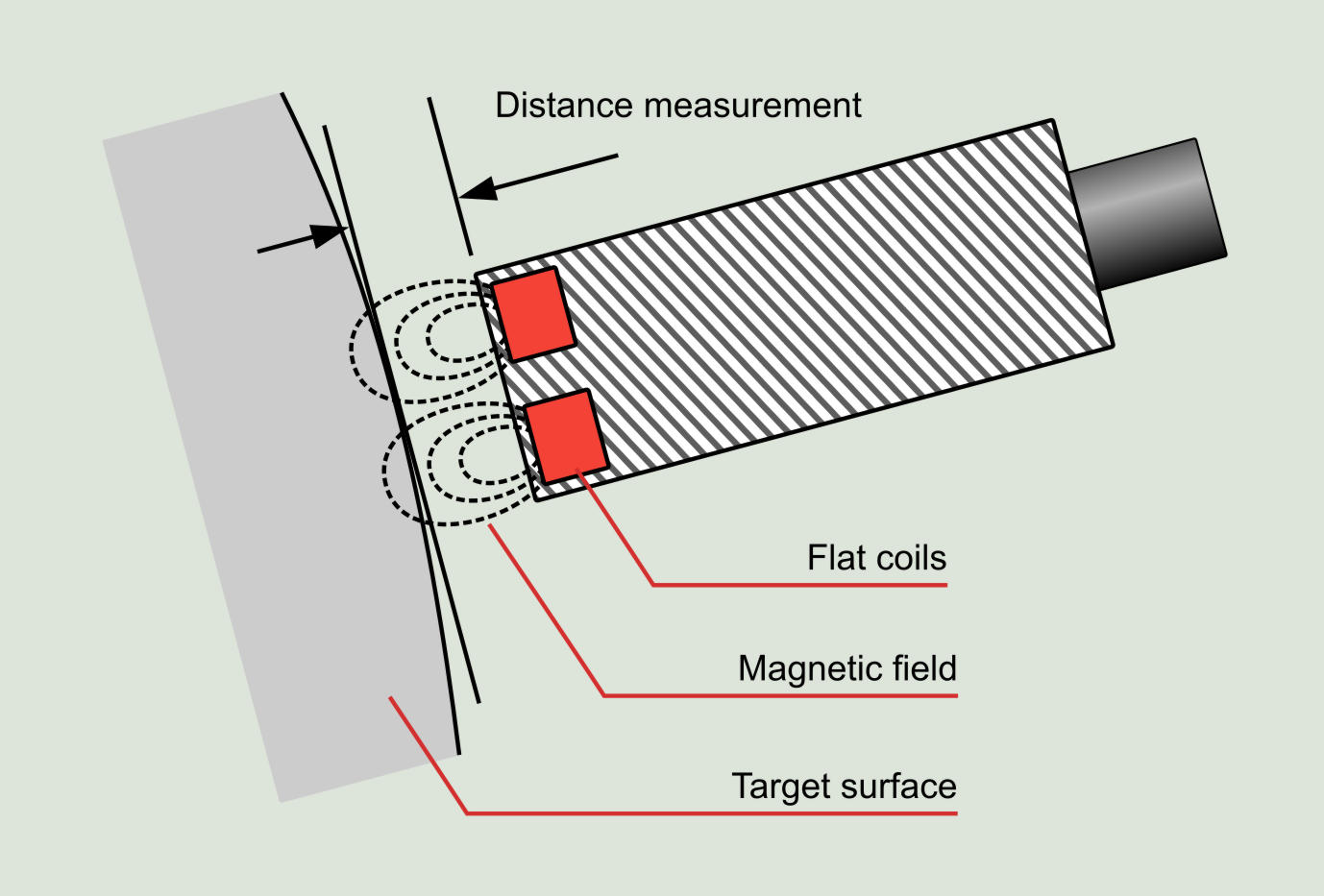
They are installed in or on the bearing caps and detect the displacement of the shaft in relation to its rest position. An Eddy type proximity pickup system consists of the sensor itself and a signal conditioner. Its frequency response is excellent. They do not have a working frequency lower limit and are used in the measurement of shaft vibration, shaft axial position and casing expansion.
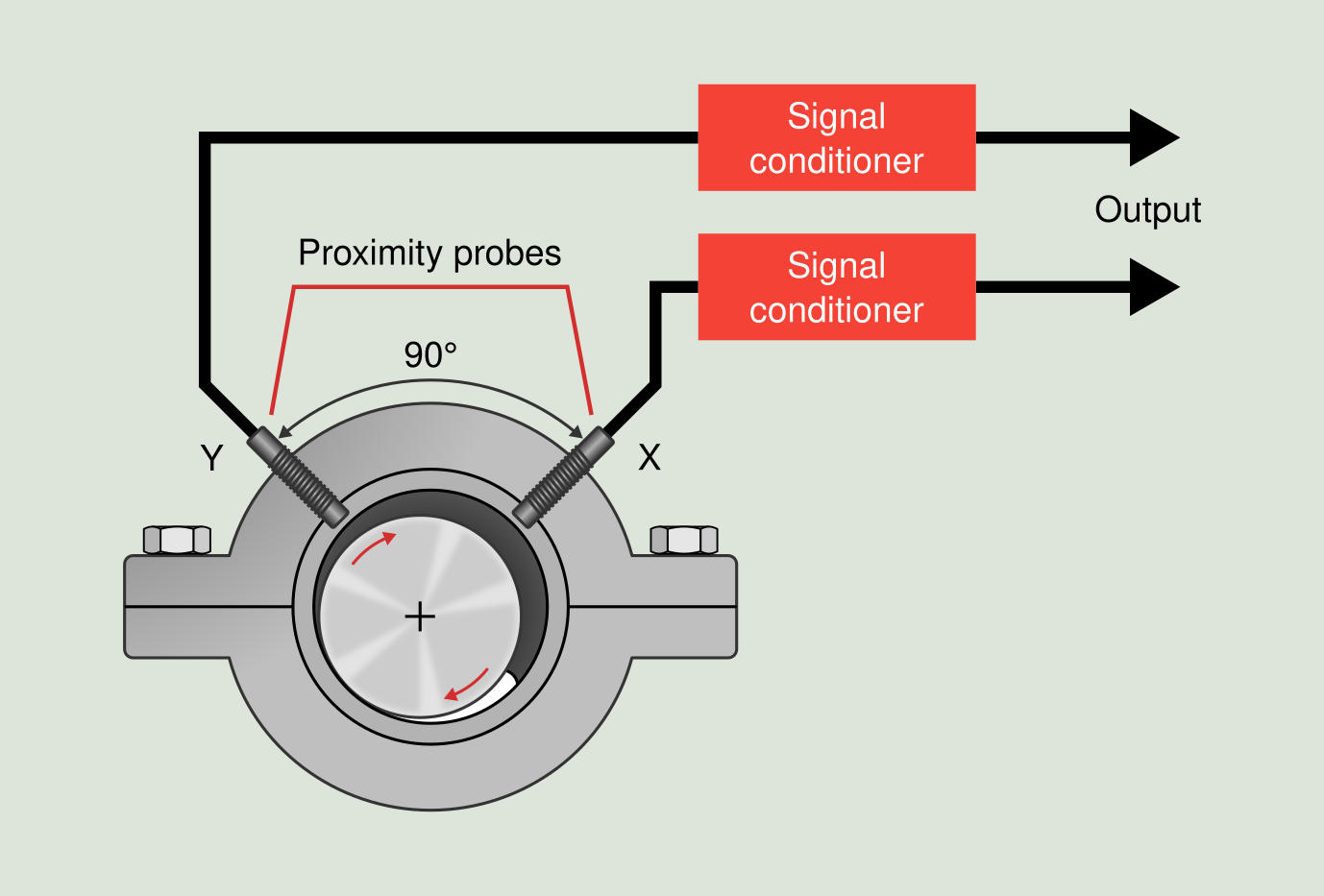
Advantages of the displacement transducer:
- It measures the relative movement between the sensor tip and the rotating shaft.
- It is particularly useful in rigid machinery where very little vibration is transmitted from the shaft to the machine casing. This situation occurs if the mass of the housing is of the same order of magnitude or higher in comparison with the mass of the shaft.
- It measures both the continuous and alternating component of a vibration signal. The continuous voltage allows physically locating the shaft inside the bearing housing under analysis. The alternating voltage provides information on the waveform and the vibration spectrum, which allows the diagnosis and monitoring of the evolution of any mechanical issues.
Disadvantages of the displacement transducer:
- These transducers must be permanently installed. This is always costly, and even impossible in certain cases.
- The frequency range is somewhat limited to between 0 Hz to 1,000 Hz.
- A signal conditioner is required.
- The displacement transducers are affected by electrical and mechanical reading errors know as slow roll. Even small cracks in the shaft can make the transducer interpret them as a high vibration activity.