New Safety Recommendations for COVID-19 in Maintenance Departments
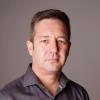
The recommendations and tips are developed for actions in the manufacturing, power generation, and heavy industries. This guidance must be implemented in conjunction with OSHA Standards and for specific industries (29-CFR-1910 Subpart I-Personal Protective Equipment standards in general industry, 29-CFR-1910.134 Respiratory Protection standard, 29-CFR-1910.1030 Bloodborne Pathogens).
These frameworks can be used by local or state health and industry departments for preparation and mitigation of workplaces. Selection and implementation of the actions must be guided and reviewed by the local characteristics of disease transmission, demographics, and public health and healthcare system capacity. To slow or halt viral transmission, the feasibility and implications of strategies for suppression and mitigation must be rigorously analyzed.
Coronavirus Disease (shortly called COVID-19) causes Middle East Respiratory Syndrome (MERS) and Severe Acute Respiratory Syndrome (SARS) which ranges in consequences from mild to fatal. The coronavirus is a large family of viruses that causes illness ranging from the common cold to fatal MERS and SARS. The virus causes severe infection in the nose, sinuses, upper throat, and lungs.
World Health Organization identified the SARS-CoV-2 in early 2020 a new virus right after the outbreak in China in December 2019. Outbreak briskly spread around the globe and to date, no vaccine is firmly developed for the cure. The spread is believed from wild animals and then person-to-person (in form respiratory droplets released by laughing, coughing, or sneezing or direct contact). On March 11, 2020, The World Health Organization have announced the unprecedented conditions as “Pandemic” considering global effects on countless lives, devastating economies, disrupted supplies, and chocking off demands.
Risks in Maintenance Teams
In volatile and uncertain times, no company/industry is immune to the devastating impacts of COVID-19. There is uncertainty among every worker around the globe. Nevertheless, the manufacturing industry is under high risk from the pandemic. As the regular maintenance of equipment is an essential part of safe work, environment, and reliable machines, the absence of maintenance can lead to a precarious situation. Maintenance in generic is a verity of tasks (Inspection, testing, measurement, replacement, adjustment, repair, upkeep, fault detection, replacement of parts, servicing, lubrication, and cleaning) in every industry sector with all types of working environments. As the lifecycle of COVID-19 is highest on metals as compared to other surfaces, maintenance workers are more likely than other employees to be exposed to hazardous situations of COVID-19. From the aspect of maintenance, the risks involved are:
- Exposure to viral workplace Environments with respiratory droplets
- Exposure to vulnerable routes for traveling to workplace
- Contact with Infected raw material/ tool/ equipment/ machinery
- Infected and enclosed working (contaminated) area without fresh air
- Infected co-workers
- Distance compromising work situations
- Stored contamination discharge
Effects
The effects of hazardous situations vary with circumstantial factors but the most common of them are:
- Absenteeism
- Low morale
- Fear
- Decreased productivity
- Lost working hours
- Spread of disease
Workplace Evaluation
As hazard recognition and control are obligatory under the regulations, workplace risk assessment for COVID-19 spread must be conducted by a competent person. Based on the facts, COVID-19 infected person in the workplace, any equipment/ tool/ machinery brought from an infected place, any crew member relating to infected family or friend member, number of personnel with symptoms, the density of COVID-19 cases in surrounding areas, workplace hygiene facilities, worker exposure to the infected area in their living facilities, hygiene facilities in canteen/ rest areas, sanitization facilities at access/ egress, and decontamination facility/ frequency of workplace, healthcare services/ capacity in the region, the workplaces can be categorized as:
- Very high risk
Working on suspected, or confirmed infected medical or healthcare facility machinery/ tool/ equipment with rare decontamination/ sanitization has a very high potential of risk. The probability of exposure to the virus is very high in these areas. Special procedures, precautions, SOPs, and plans must be developed and implemented with the most effective efficiency.
- High risk
Working on healthcare laboratory machinery/ tool/ equipment, medical facility services (ambulances, wheelchairs, etc.), must be categorized as high-risk areas. Periodic decontamination/ sanitization on precautionary measures must be ensured.
- Medium risk
The workplaces of suspected (isolated for testing) personnel with symptoms, areas of close contact (less than 6 feet) with unsuspected people, contact with the general public (schools, high-population-density environments, high-volume retail services) must be categorized as medium risk.
- Low risk
The area confirmed with NO-Suspected person (no contact with people), or machinery/ tool/ equipment with efficient sanitization or decontamination facilities must be low risk in the categorization.
Equipment and Tools Risks
As the life span of COVID-19 is 2-3 days on stainless steel, the potential risk of COVID-19 exacerbates in manufacturing, power, and heavy industries. The use of tools, equipment, and machinery suspected for virus infection needs more attention. The life span on glass is 4 days which must also be considered in manufacturing industries as the glass products are used.
If any confirmed case found in the workplace, the work whole group becomes suspicious and must be isolated according to CDC recommendations. In the situation of maintenance of equipment/ machinery from the healthcare facility, very high-risk values are exposed.
Work Habits Changes/ Recommendations
Although the interim guidance and procedures are developed from the regulating authorities, the recommendation inhere must be followed in conjunction.
Handwash/ Sanitization |
Frequently wash your hands with soap and water for at least 20 seconds. If soap or water not available, use alcohol-based hand rub that contains at least 60% alcohol. |
Social distancing |
Maintain 2-meter distance wherever possible, including while arriving, departing from work, while in work, and when traveling between sites. |
Self-isolation |
Anyone having symptoms of COVID-19 (fever, cough, fatigue, shortness of breath), or working/ living/ close contact with someone having symptoms, should not come to worksites and follow the instruction on self-isolation. |
The person at increased risk |
The persons with low immunity or other vulnerable medical conditions to COVID-19 must stay at home and should minimize contact with suspected conditions. |
Persons defined on medical grounds as extremely vulnerable |
Anyone identified as extremely clinically extremely vulnerable will be advised by their health authority and must follow the guidance on shielding and protecting people who are clinically extremely vulnerable from Covid-19. |
Living with a person in one of the above groups |
Anyone living with a person who is at increased risk of severe illness, or an extremely vulnerable person who is shielding from Coronavirus (Covid-19), should stringently follow the guidance on social distancing and minimize contact outside the home. |
If someone falls ill |
If a worker develops a high temperature or a persistent cough while at work, they should:
They must then follow the guidance on self-isolation and not return to work until their period of self-isolation has been completed. |
Traveling to work
In case if the remote work from the offsite location is not possible, the workers must follow the guidelines outlined here.
- Frequently check body temperature.
- Wherever possible workers should travel to the site alone using their transport.
- If workers have no option but to share transport:
- Journeys should be shared with the same individuals and with the minimum number of people at any one time
- Good ventilation (i.e. keeping the windows open) and facing away from each other may help to reduce the risk of transmission
- The vehicle should be cleaned regularly using gloves and standard cleaning products, with particular emphasis on handles and other areas where passengers may touch surfaces.
- Parking arrangements for additional vehicles and bicycles.
- Other means of transport to avoid public transport e.g. cycling.
- Providing hand cleaning facilities at entrances and exits with hand sanitizer, if soap and water are not available.
- In the case of public transport:
- Changing and staggering site hours to reduce congestion on public transport
- Avoid using public transport during peak times.
Driving at Work
- When traveling at work or between site locations, workers should travel alone.
- Frequently check body temperature.
- If workers have no option but to share a vehicle, then they should:
- Share with the same individuals and with the minimum number of people at any one time.
- Wherever possible maintain a distance of two meters and avoid touching their faces.
- Maintain good ventilation (i.e. keeping the windows open) and face away from each other during the journey.
- Wash their hands for 20 seconds using soap and water or hand sanitizer if soap and water are not available before entering and after getting out of the vehicle.
- Regularly clean the vehicle using gloves and standard cleaning products, with particular emphasis on handles and other surfaces that may be touched during the journey.
Site Access and Egress Points
- Stop all non-essential visitors.
- Consider introducing staggered start and finish times to reduce congestion and contact at all times.
- Check the body temperature of personnel entering the facility.
- Plan site access and egress points to enable social increase/decrease number of access points to enable monitoring, including in the case of emergencies.
- Introduce one-way systems.
- Allow plenty of space between people waiting to enter the site (At least 2 meters).
- Use signage:
- Such as floor markings, to ensure 2-meter distance is maintained between people when queuing.
- Reminding workers not to attend if they have symptoms of Coronavirus (Covid-19) and to follow guidelines.
- Remove or disable entry systems that require skin contact (e.g. fingerprint scanners) unless they are cleaned between each use.
- Require all workers to wash their hands for 20 seconds using soap and water when entering and leaving the site.
- Regularly clean common contact surfaces in reception, office, access control, and delivery areas e.g. scanners, turnstiles, screens, telephone handsets, and desks, particularly during peak flow times.
- Reduce the number of people in attendance at site inductions and consider holding them outdoors wherever possible.
- Where loading and offloading arrangements on-site will allow it, drivers should remain in their vehicles.
- Where drivers are required to exit their vehicles, they should wash or sanitize their hands before handling any materials.
Hand Washing
- Allow regular breaks to wash hands/ sanitization.
- Provide additional handwashing facilities (e.g. pop-ups) to the usual welfare facilities.
- Ensure adequate supplies of soap, fresh water, and sanitizer are readily available and kept topped up at all times.
- Provide hand sanitizer (minimum 60% alcohol-based) where handwashing facilities are not possible.
- Regularly clean the handwashing facilities.
- Provide suitable and sufficient rubbish bins for hand towels with regular removal and disposal.
Toilet Facilities
- Restrict the number of people using toilet facilities at any one time and use signage, such as floor markings, to ensure 2-meter distance is maintained between people when queuing.
- Wash or sanitize hands before and after using the facilities.
- Enhance the cleaning regimes for toilet facilities, particularly door handles, locks, and the toilet flush.
- Portable toilets should be cleaned and emptied more frequently.
- Provide suitable and sufficient rubbish bins for hand towels with regular removal and disposal.
Canteens and Rest Areas
- Where possible, workers should be encouraged to bring their food. They should also be required to stay on-site once they have entered it and avoid using local shops.
- Where no alternatives for workplace canteens,
- Provide food to staff with appropriate adjustments for social distancing.
- Canteens should provide a takeaway service providing pre-prepared and wrapped food only.
- Consider increasing the number or size of facilities available on-site if possible.
- The capacity of each canteen or rest area should be identified at the entry to each facility.
- Break times should be staggered to reduce congestion and contact at all times.
- Disposable Drinking water should be provided.
- Frequently clean surfaces that are touched regularly, using standard cleaning products e.g. kettles, refrigerators, microwaves, etc.
- Hand cleaning facilities or hand sanitizers should be available at the entrance/ exit to be used by workers when entering and leaving.
- A distance of 2 meters should be maintained with reconfiguration to reduce face to face interactions.
- All rubbish should be put straight in the bin.
- Tables should be cleaned between each use.
- Crockery, eating utensils, cups, etc. should not be used unless they are disposable or washed and dried between uses.
- Payments should be taken by contactless cards wherever possible.
- The canteen staff should use disposable gloves and wash their hands often with soap and water for at least 20 seconds before and after handling food.
- Canteen staff and workers may use the same rest areas if they apply the same social distancing measures.
- Consider arrangements for monitoring compliance.
Changing Facilities, Showers, and Drying Rooms
- Consider increasing the number or size of facilities available on-site if possible.
- Based on the size of each facility and maintain a distance of two meters.
- Restrict the number of people using these facilities.
- Introduce staggered start and finish times to reduce congestion and contact.
- Introduce enhanced cleaning of all facilities throughout the day and at the end of each day.
- Provide suitable and sufficient rubbish bins in these areas with regular removal and disposal.
Personal Protective Equipment
Correct use of PPE can help prevent exposure, but it should not take the place of other prevention strategies, whenever possible. The types of PPE required during a COVID-19 outbreak will be based on the risk of infection while working and the tasks that may lead to exposure. During an outbreak of an infectious disease such as COVID-19, recommendations for PPE specific to occupations or job tasks may vary depending on geographic location, updated risk assessments for workers, and information on the effectiveness of PPE in preventing the spread of the virus. Examples of PPE include gloves, goggles, face shields, face masks, gowns, aprons, coats, overalls, hair and shoe covers, and respiratory protection, when appropriate.
To be effective, PPE must be selected based upon the hazard to the worker; properly fitted and periodically refitted; worn consistently and properly when required; regularly inspected, maintained and replaced as necessary; and properly removed, cleaned and stored or disposed of, as applicable, to avoid contaminating the worker, others or the environment.
Type of device | Description | Standards | |
---|---|---|---|
INSTRUMENT
|
Infrared thermometer | Electronic thermometers that assess the temperature by determining the intensity of infrared light emission. |
|
PPE
|
Gloves | Gloves, nitrile, powder-free, non-sterile. (minimum thickness 0.05mm) |
|
Face shield | Made of clear plastic, provides good visibility, Adjustable band to attach firmly, Fog resistant (preferable), Completely cover the sides and length of the face, Maybe reusable or disposable. |
|
|
Fit Test Kit | To evaluate the effectiveness of seal for tight-fitting respiratory protection devices |
|
|
Particulate respirator, grade N95/FFP2 or higher | N95 or FFP2 respirator, or higher Good breathability with a design that does not collapse against the mouth (e.g. duckbill, cup-shaped) |
|
|
Gown | Single-use, non-sterile, disposable, length mid-calf. |
|
|
Alcohol-based hand rub | Bottle of 100ml & 500ml, at least 80% ethanol or 75% isopropyl alcohol (v/v) | Required:
|
|
Soap | Liquid (preferred), powder and bar |
What is Power-MI?
Power-MI is a cloud based solution that allows you to design & manage your condition-based maintenance plan integrating all techniques into one platform. Easy reporting, automatic work orders and CMMS integration.
Read more