Digital Disruption in Asset Management
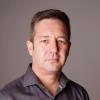
The impact of Industry 4.0 and the Internet of Things (IoT) on asset management has already been discussed. In this article we will analyze these two concepts in light of the new technologies that will directly affect asset management and the impact these digitalization processes will have on asset management.
To begin, a little history
The concept of Industry 4.0 is something that over time has resulted in different interpretations especially in commercial usage. The origin of the Industry 4.0 concept is the introduction of a strategic initiative of the German government to help factories to be digitized. This initiative was presented for the first time at the Hannover Fair in 2011. The idea was to form a group of academics and industrial leaders to generate lines of action for the digital transformation of industries.
The suffix "4.0" refers to the fact that we conceptually identify this digitization process as the fourth industrial revolution.
The first industrial revolution began in England in 1765 with the incorporation of the steam engine, breaking into agriculture and transport. The second industrial revolution began in 1870 with the incorporation of the electric motor into production processes, allowing mass production. And in 1969, IT was incorporated into industry through controllable logic programmers (PLC), which allowed the automation of production processes. This is considered the third industrial revolution.
As steam led to the first industrial revolution, power to the second industrial revolution, and controllable logical schedulers to the third, the elements that characterize the fourth industrial revolution are the cyber-physical systems.
The Fraunhofer-Institut describes the concept of the cyber-physical system according to the attached image. First, we see parts of a cyber-physical system: the user interface, the actuators, the sensors and other cyber-physical integrated systems. Likewise, each cyber-physical system has its own interfaces in internal and external communication as well as management systems.
Now, what is the IoT? IoT stands for Internet of Things also called by the same name in Spanish. The internet was conceived as a means of connecting people through the agile transmission of data. As more services are introduced such as file sharing, music and video consumption, and video calls, such processes have had to increase the communication protocols from 2G to 3G and then to 4G.
Thus, the concept of the evolving IoT itself tells us that it is no longer about communicating with people; now it’s the turn of "things" to communicate with each other. Traditionally, this concept was applied to cell phones, smart wristbands, home sensors. Now, the industry is taking part of the internet to communicate among cyber-physical spaces. That's why many prefer to talk about IIoT (Industry Internet of Things). This incorporation of huge amounts of data between cyber-physical spaces has demanded what has been eagerly awaited: the 5G, which will notably favor communication within cyber-physical spaces.
In summary, Industry 4.0 is the concept that describes the dawn of a new industrial era and the IoT is the facilitator of this era.
What technologies are breaking into asset management?
From a general perspective, the technologies that break into asset management are all those that allow digitizing the operations or conditions for managing that information.
Thus, we can regard sensors as the first line of disruption. While sensors have been around for decades, hardware prices are now falling. In fact, for the equipment and sensor manufacturers, the big point of disruption is that the value of their business is moving from hardware to data. This touches the core business of several companies.
But not only are the prices of sensors falling. We also see developments such as the incorporation of MEMS type sensors used to monitor the mechanical vibrations of rotating machinery and operate on low energy, which perfectly accommodate the switch to wireless applications.
Today there are already companies that allow online digitizing of the condition of oil through particle recognition for both offline database analysis and charting. Such sensors were simply inconceivable a few years ago.
Another example of new technologies applied to the monitoring of assets is the incorporation of drones in the visual inspection of high power lines with their respective image processing leading to automated routines. This same technology is also used for monitoring civil works and wind turbines.
The Blockchain, another technology used for financial transactions, will have a huge impact on the management of spare parts to provide traceability to the supply chain. This means we can know where each piece was made and where it has gone, even what margin has been charged for each transaction. Transparency in the supply will now be in the hands of suppliers who often base their value on information asymmetry, that is, on not revealing the origin and links of the supply chain of what they are selling.
Again, cloud computing now allows assets to be managed centrally. In monitoring conditions in the past, information concerning assets was managed separately depending on the technology used and who handled the analysis (own staff or service companies). Reports of asset inspections were delivered in different formats, with different criteria and with little quality control. The bottom line is that asset managers simply want to know the condition of the assets are and what needs to be done. Thus, the company that I represent (Power-MI) allows management to centralize all inspection technologies by standardizing not only the format but also the analysis criteria using a catalog of failures. Thus, control panels can be generated for asset managers.
This augmented reality allows both remote support and the protocolization of visual inspections of assets, improvement of documentation and substantial improvement in the training of technicians and asset operators. Additive manufacturing and 3D simulation are two other technologies that will have a direct impact on the supply of asset components.
Last, but not least in asset management, is the incorporation of Machine Learning in. Machine Learning is the technology that takes all of an asset’s available data and, upon analysis, converts it into key information for decision-making. Players in the race to compete in this new market are Microsoft Azure, IBM Watson and Predix, among others. Machine Learning is the technology par excellence to pave the way for Artificial Intelligence (AI). The tendency is for these algorithms to learn from data and tags so that the condition of an asset can be automatically diagnosed later, together with an evaluation of the quality of a product or the demand for the use of an asset.
Effects of digitization on asset management
First, let's look at the impact from the user’s perspective. If we look at the image of cyber-physical spaces, we will see two axes: an axis of vertical integration and a horizontal one. Both have their own meanings.
Vertical integration involves the interconnection of cyber-physical spaces at all levels of the organization: from the sensors connected in an asset to the processes of management decision making. Cyber-physical spaces only make sense if their architecture allows this hierarchical functionality. This implies that asset management starts from the status of the assets converted into data, and that will have a direct impact on the decision-making of the industry, company or organization.
Horizontal integration involves the interconnection of cyber-physical spaces at the same hierarchical level. Thus, asset performance indexes can be compared between different production lines, departments or zones. However, this is no longer confined to equivalents within an organization or company. Now the cyber-physical spaces can also interconnect with those from different companies.
This horizontal integration between the cyber-physical spaces of different companies is one of the greatest impacts in the management of assets since plants can be compared despite belonging to different companies. This inevitably leads to the "anonymization" of data.
I remember when I was working with General Electric as a client in monitoring projects for their cogeneration plants, I could see the value they obtained by comparing the performance of different plants with similar structure and configuration. This comparison was exclusively for large corporations that owned several similar plants on their property. Now, with the digitalization and the possibility of interconnecting data anonymously, the comparison between plants ceases to be an exclusive functionality of these corporations. And that is precisely why we are talking about another industrial revolution!
Another important characteristic is transparency. This, more than a consequence, is really a requirement. Every digitization process implies a process of transparency in the management of assets. This is often a sensitive issue in many organizations as it is directly linked to their business culture. In companies with a hierarchical internal culture and one where staff feel constantly threatened, data and information are often used as a hidden letter to internally negotiate responsibilities and decision-making. Digitization can only create value in companies whose internal culture promotes transparency in the operations.
Both the horizontal integration of information and the implicit transparency of digitalization lead to another consequence, and that is to discharge silos of “proprietary” information. Large companies commonly form islands of information in which information of common interest hardly flows from one place to another. Digitization, in the context that we explain here, demolishes these islands of information.
A maintenance manager once told me in the preparation of a case study that in the past the maintenance department staff interacted only with production and eventually with purchases. From the gradual process of digitization, he could see how little by little the maintenance department had to integrate IT (computing), R & D, quality control. This enabled better control as different departments began to exchange indicators and rotate personnel for specific operations, thus making possible an authentic transfer of knowledge driven by the sharing of data.
At the technical level, digitalization processes will make reliability a relevant feature in asset management.
The dilemma of the asset manager
As mentioned, artificial intelligence is becoming more relevant in asset management. Machine Learning requires both structured data and labels. Let's look at a simple example.
Let’s say we want to monitor an industrial pump using vibration sensors and permanently installed temperature probes. We take that data to an OPC server where we have the option of receiving the pump operation data: pressure and flow. All this data synchronized over time is used in MS Azure to make a series of correlations in multiple dimensions, that is, by contrasting different variables using different correlation methods. This is a Machine Learning process.
There are two types of Machine Learning algorithm: non-supervised and supervised. The non-supervised ones are based on normality curves, that is, the normal behavior of the asset is obtained empirically. In general, this requires a lot of data and research and the level of certainty of the diagnoses is very low.
Supervised algorithms, on the other hand, require tags or labels. These labels, for our example, could be the status of the asset and, in the case of a fault detected, the fault or cause of the fault. Providing the algorithm with several labels has the advantage of ensuring that learning is faster and the level of certainty of the diagnoses automatically generated is higher.
At the beginning, the labels must be entered by the asset manager and this is where the dilemma comes in: will the asset managers feed the monster that will later eat them? That is, can artificial intelligence replace maintenance managers once they are able to automatically detect the condition of assets and generate work orders to improve the reliability of assets?
In fact, this dilemma applies not only to Machine Learning but also to all other 4.0 technologies whose implementation requires the intervention of asset managers. Each person can reflect on the implications for them, but in my opinion, the impact of digitization in the management of assets with respect to personnel is that job functions will have to evolve a lot further. For the time being, it is premature to describe the new functions that asset managers will have, but it is evident that they will be much more sophisticated than the current ones and the need for a paradigm shift is without question.
What is Power-MI?
Power-MI is a cloud based solution that allows you to design & manage your condition-based maintenance plan integrating all techniques into one platform. Easy reporting, automatic work orders and CMMS integration.
Read more