How to Define the Vibration Alarm Limit of a Machine (and Not With ISO Charts)
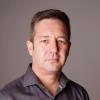
One of the essential tasks of a vibrations analyst is defining the acceptable global vibration limit to determine the condition of the machine. We are going to tell you what the experts do, and it is not by using ISO charts.
The vibration levels must be determined according to the following criteria:
Taking the history of the machine as the baseline
If we have data of the machine, previously taken in a constant manner, and we know the condition of the machine during that period, that is the best source of information to determine the alarm limits. Predictive maintenance engineers determine such alarm levels by obtaining (visually or by hand calculation) the vibration reading of the machine in good conditions plus an acceptable deviation.
The acceptable deviation of the machine is between 10% and 50%, and it will depend on the vibration peaks in the tendency of the machine. A machine with stable global vibration levels in the calendar time must have an acceptable deviation lower to that of a machine with many vibration fluctuations.
This criterion, although the most accurate, has certain disadvantages: (1) it has to be done on each particular machine (and each point), and it can take a lot of time if we have a big machine pool; (2) it requires information and knowledge of the machine over a long period of time, something that is not always accessible.
Advice: ask your vibration data collector provider or the provider of the vibration analysis software if they have an alarm set function. Some software programs have this function where you just have to select the acceptable deviation, and the alarm levels are automatically defined.
Good conditions test and acceptance analysis
Many times, we have to analyze a machine for the first time, either because it is just installed or because it has been recently repaired. In these cases, we count on a report of the repairs and start-up where it can be verified if the machine has been repaired and started in operation conditions. What the vibrations analyst must do is the acceptance test to determine if, in fact, the machine does not show any abnormal signals.
One of the results of the acceptance test is the acceptable alarm limits for that machine. For those, the analyst focuses on the history of the machine. Or if he does not have any other information, the analyst focuses on the readings obtained. The analyst recommends taking at least three readings to see the variations in the vibrations and, based on that, determining the alarm level. Likewise, it is important to consider the recommendation of the manufacturer, although, in case of doubt, our criterion based on the readings must prevail.
Recommendations of the machine manufacturers
Some manufacturers determine the acceptable vibration alarm limits. This gives us a good initial reference. However, we must opt for creating our own knowledge base to later adjust that alarm level.
Many field engineers consider that the alarm levels of the manufacturers are too conservative, although we do not recommend increasing the alarm limits of the manufacturers in our analysis software without a previous analysis of the machine and without having a history of the data and the maintenance tasks.
Twin machines
When we do not have the information of the machine, but there is another unit which is the same or similar, we can take that one as the baseline to have an understanding of the acceptable vibration levels. This technique is used by analysts to also determine the spectral patterns.
Remember that the operational conditions and the environment can affect the vibrations in a different way for each machine. Do not extrapolate the alarm levels of a machine to another without the commitment of verifying and adjusting such alarm levels afterward.
Acceptable vibration levels charts
We can find regulations, recommendations of professional associations where acceptable vibration levels are set. This works well when none of the options previously explained are feasible. Use those charts only when there is no other reference.
What is Power-MI?
Power-MI is a cloud based solution that allows you to design & manage your condition-based maintenance plan integrating all techniques into one platform. Easy reporting, automatic work orders and CMMS integration.
Read more